Construction plays a pivotal role!
- An excellent operator can improve the performance of drilling rigs, protect components, prevent hidden dangers, reduce construction costs, reduce fuel, noise and emissions, create benefits for customers, and enhance corporate image through operation. Construction plays a pivotal role!
The operation can be divided into three parts: the auxiliary condition, the main condition and the detection. Today, let’s talk about the main condition
The main working condition is mainly drilling. Because the drilling rig is constructed in a concealed project and the geology is changeable, the drilling in the main working condition requires more experience and technology, and also requires more attention.
1 Positioning:
1.1 Pad crawler: Before positioning, the position of the pile should be clearly defined, and the site conditions should be carefully observed. It should be located in a position where the terrain is flat, the machine is easy to move back, and the slag is easy to remove. Soil pad crawler, not only to make the crawler firm, it is better to make the drilling rig close to the horizontal state, which is helpful for operation control, especially the turning and dumping of slag is very smooth
1.2 Guided piles: Guided piles play the role of drilling rig positioning and protection and positioning. There are two methods of nailing the guide pile
1.2.1 Center alignment: randomly lead out a certain distance around the pile position to place 4 guide piles, as long as the center of the cross line is aligned with the pile position, after the protective tube is placed, pull the cross line well, and measure the deviation of the protective tube, This method of nailing and guiding piles is simple and random, but it is only suitable for good geology and short casing.
1.2.2 Setting of guide pile: Another method is to keep a certain distance between the guide pile and the pile position. During the current protection, the deviation can be calculated by subtracting the radius of the guard tube from the distance between the guide pile and the pile position, so the current protection You can use a meter ruler to measure and direct the adjustment. When the protective tube completely falls into the hole, the positioning of the protective tube is basically completed. This method is a bit cumbersome, but it corresponds to the complex geology, and the lower protective tube is helpful. It should be said that This method is the quickest and correct
1.3 Drilling rig positioning: After the crawler pads are cushioned and the reticle is pulled, first lock the travel, then level the mast, position the drill bucket and the reticle through rotation and luffing fine-tuning, and then clear the rotation and depth, and Switch the luffing to pressurization to open the hole
2 lower guards:
2.1 Drilling: Since there is no hole wall guide, the opening should be controlled by floating and slow footage, and the self-weight of the drill pipe can be used to drill to prevent excessive deviation of the opening and affect the positioning of the casing
2.2 Reaming: The purpose of reaming is to embed the casing, so before reaming, it is necessary to know the diameter and length of the casing, check whether the length of the reamer can meet the requirements, and inform the auxiliary personnel to use a meter ruler to measure the reaming depth. There are two methods of reaming: 1. Reaming while drilling. This method has fine reaming, accurate positioning, and is suitable for most geology, but the load is large. 2. Drill to a certain depth first and then use a reamer to ream the hole. This method It is suitable for better formation and lower short casing, convenient and fast, light load, but not suitable for complex formation, especially hard formation. Under normal circumstances, the diameter of the reaming hole should be 5 to 10CM larger than the diameter of the casing, and the spacing between the casings should be reserved.
2.3 Lower guard: under normal circumstances, the length of the guard is 2 to 3 meters, the diameter is greater than the pile diameter of 20CM, and the thickness of the steel plate used for the guard is more than 10MM. There must be a ring of reinforcing ribs around the top edge of the guard. It needs to be hoisted, so two round holes need to be cut on the symmetrical sides of the protective top to be the hanging points. When cutting the two hanging points, one must be symmetrical and the height should be the same. It is best to use two steel wire ropes with the same length to lift. The protective tube can ensure the verticality and deviation of the protective tube. The bottom edge of the protective tube is pressed into the geological 10 to 20CM, the upper edge of the protective tube is 20CM higher than the ground, the deviation range of the protective tube is within 5CM, and the vertical deviation of the protective tube is 1% degree.
3 Drill in:
3.1 Geology: Before drilling, it is necessary to understand the type and distribution of the geology, the main thing is the strength of the geology, the geological ultimate bearing capacity, as well as the groundwater level and the pile diameter and depth can be obtained through the geological report and core sampling. Only by fully understanding the geology After the conditions are met, the mud can be prepared, equipped with drill pipe drilling tools and gears, and the corresponding operation methods can be used.
3.2 Mud: Mud plays the role of protecting the drilling rig and ensuring the quality of the hole. After understanding the geological report, according to the type and distribution of the geology, combine the geological strength and the requirements of Party A to prepare the mud. The quality parameters of the mud include: viscosity, specific gravity and Sand content, the role of mud includes: wall protection, support, lubrication, suspension, cooling and buoyancy, the most important of which are the first two points of wall protection and support
The support wall uses the viscosity of the mud, and the support uses the specific gravity of the mud. In most cases, as long as the wall protection effect is achieved, the construction can be satisfied, and the water itself has a specific gravity, and as the depth increases, the water pressure increases. The water pressure of the casing is the lowest, so the viscous protective wall is used in the casing to make up for the water pressure. It can be seen why the mud casing is not good, and the surrounding of the casing is easy to collapse. If the mud is not prepared according to the geological requirements, it will cause hole collapse, sediment, buried drilling, pinching and other phenomena.
3.3 Drill pipe: After understanding the geological conditions, the drill pipe should be equipped according to the pile diameter, pile depth and geological strength. The drill pipe is divided into friction resistance and machine lock. The machine lock rod can drill into high-strength geology, but requires machine lock and To unlock, you must first understand the position and spacing of the machine lock points, combined with the current drilling depth, and then lift or lower the power head to quickly find the lock point. When the machine locks, the drill bucket is required to provide resistance, if the resistance of the drill bucket is smaller than that of the drill pipe Due to the friction of its own weight, there will be a phenomenon that the machine cannot be locked due to slippage. Unlocking also requires the drill bucket to provide resistance, so it is best to reverse the unlocking when the drill bucket has resistance. The premise of reversing reduces the friction of the machine lock point, and the sequence of unlocking is from the inside to the outside, that is, starting from the drill bucket. , and finally the power head is unlocked. When lifting the drill, it can be determined whether each section of drill pipe is retracted through the impact sound and lifting resistance of each section of drill pipe retraction, so as to prevent the phenomenon of carrying rods. The friction-resistance drill pipe mainly drills into ordinary geology, and provides frictional force through resistance. It is characterized by fast lifting and lowering speed, low probability of carrying rods, and more than machine-locked rods.
3.4 Drilling tools: The performance of the drilling rig, the ability of the team, and the skills of the operator are finally condensed on the drilling bucket. Therefore, it can be seen that the drilling bucket is the most important. As a operator or an after-sales person, you must master the application of drilling Tools, use drilling tools, modify drilling tools, the only way to become a qualified operator or after-sales engineer. Drilling tools and gears should be configured according to the type and strength of the geology. For example, the most common double-bottom sand bucket, the use of picks becomes a double-bottom rock entry, which can drill into harder sandstone and gravel, and use the treasure E-tooth can prevent falling off, anti-break, wear-resistant and other functions, can be suitable for
Co-drill into the pebble layer. Under normal circumstances, the use of double-bottom salvaging and double-bottom rock penetration can meet most geological construction requirements, and the resistance of the drill bucket mainly comes from the teeth and the leading tip, including the position of the side teeth, the left and right groups of canine teeth are staggered, and the teeth of the teeth are staggered. Angle, quantity, model and type, length, width and type of center pilot tip, size of slag inlet, etc.
3.5 Operation: Since the drilling rig is constructed in a concealed project, it needs rich experience to deal with various situations. When drilling, through the methods of viewing, smelling, and cutting, it is possible to know the geological changes, the situation in the hole, and change the operation method. Only in this way can Drill at the fastest speed and prevent hidden dangers
3.5.1 To look: to observe. Since the power head uses a variable motor, the rotational speed also changes with the change of the load. Therefore, the load condition can be known by observing the rotational speed of the drill pipe, and the flow rate of the mud on the drill pipe can be obtained when drilling Observe the geological conditions around the casing, and also observe whether the mud in the casing is bubbling and turning over, and whether there is sand on the girder of the drill bucket, and the difference between the depth after the second drilling and the depth when the drilling is lifted. These are all phenomena that can reflect whether there are signs of collapsed holes. Observe the type of muck poured out when pouring muck, as well as the insurance of the drill pipe pin, and observe whether the hook is fully fastened when closing the bucket door.
3.5.2 Smell: listen carefully. During operation, the sound also changes with the change of the power head and the main hoisting load. Therefore, the geological changes and abnormal situations can be known immediately through the sound, and corresponding responses can be made immediately. At the same time, you can also listen to the sound of the engine and the hydraulic system, and monitor the operation of the drilling rig in real time. When lifting or lowering the drill pipe, an impact sound will be heard after each section of the drill pipe is put out or retracted, and you can know whether there is a rod, etc.
3.5.3 Cut: Feel the vibration. During the process of rotary drilling, the load and vibration generated by the different geology will change accordingly. Combined with the load and vibration, the condition of the land in the hole can be known, so as to make different operations. Determine the geological changes in the hole at the first time, and the operation mode and drilling depth will also change accordingly. If each type of geology is an operation method, it will definitely affect the drilling speed.
Hard to even get into
3.6 Operation control: when operating the main working condition of the drilling rig, only four actions can be controlled: pressurization mode, speed, float and engine speed
3.6.1 Pressurization method: According to the type and strength of the geology, as well as the diameter of the pile and the drill pipe used, the pressurization method is divided into: continuous pressurization, point pressurization, intermittent continuous pressurization, and pressurization return. pressure, point pressure after continuous pressure
3.6.2 Drill pipe rotation speed: low-speed drilling can be used when drilling into formations with large vibration; medium-speed drilling can be used when drilling mud eggs or sand egg layers; high-speed drilling can be used when drilling into formations without low vibration load
3.6.3 Floating: the floating point can be used when opening the hole; the floating can be normally opened during normal drilling; the rear floating can be used when drilling into the strongly weathered stratum that is prone to partial hole
3.6.4 Engine speed: match the engine output power according to the load situation, so adjusting the engine speed to adjust the engine and pump output power can effectively protect the drilling rig components and save fuel, vibration and noise.
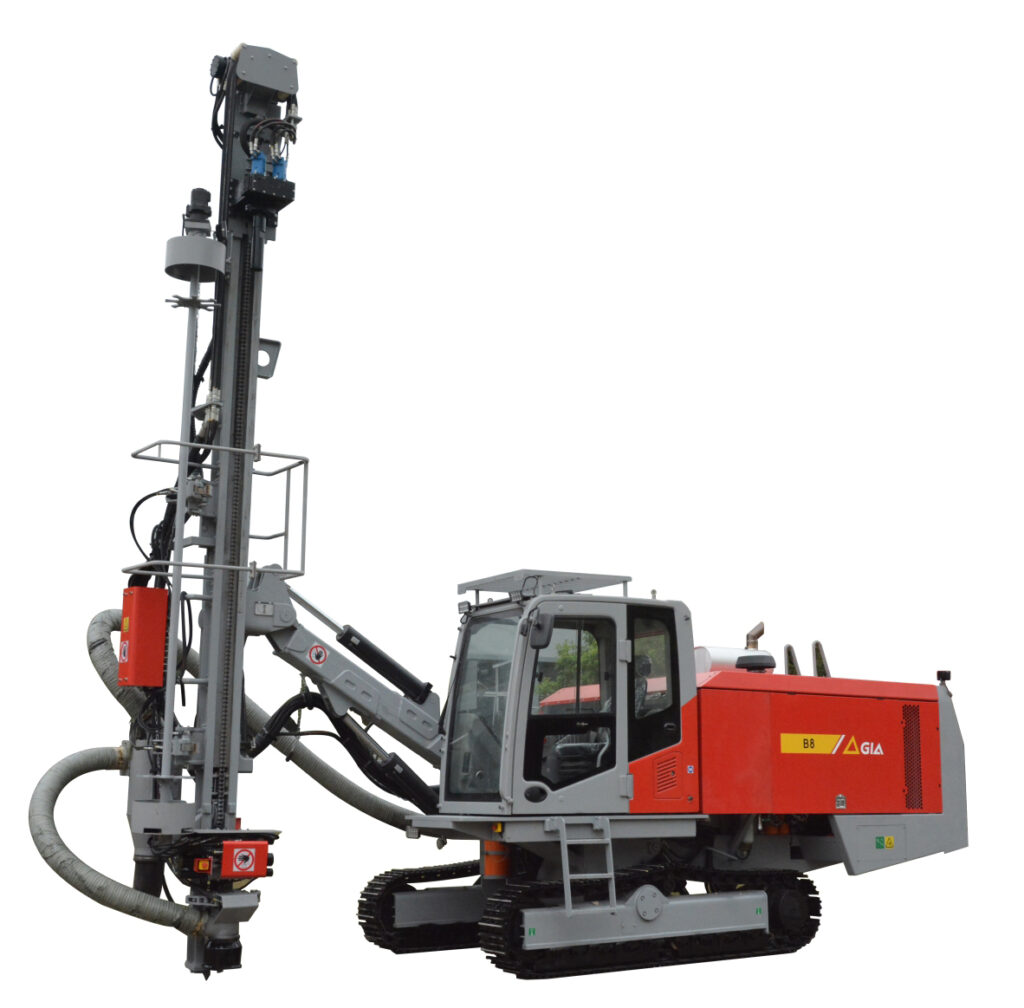